
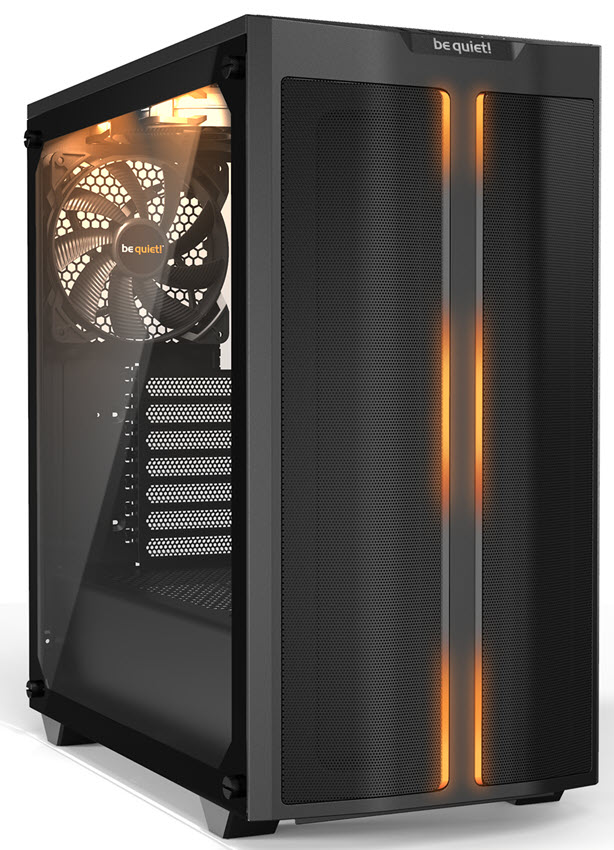
SETT was followed by four more test engines by May 2018.
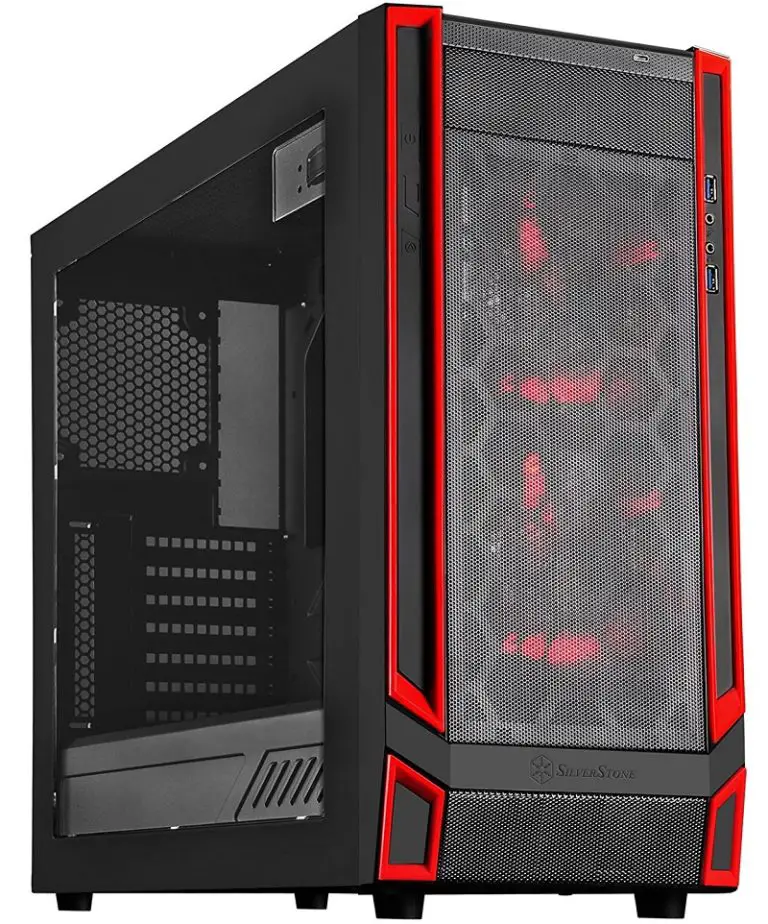
During the FAA 150 hr block test, the variable stator vane (VSV) lever arm failed and its redesign led to a 3–month delay. SETT testing started on May 16, 2017, at Peebles, Ohio, 13 months after FETT it was the first engine built to the finalized production standard for certification. The tip clearance at the front of the HP compressor was modified as a result of early running experience. ĭesign changes between FETT and second engine to test (SETT) addressed improvements required to meet efficiency goals: the minimum area in the duct between the HP turbine outlet and the LP turbine inlet was altered to set the operating line of the compressor, turbine and fan. A design change required for the GEnx was the addition of bypass doors between the booster and high-pressure compressor which open into the airflow path to reduce the chance of ice crystals entering the core. This testing improved the understanding of core icing as well as the more familiar rime ice. Simulated high-altitude conditions were used to test the GE9X for ice crystal icing (core icing) which was an issue for the GEnx. Icing certification and evaluation finished during the 2017-2018 winter at Winnipeg, Manitoba. The FETT was used for ground cold weather testing in natural icing conditions such as ground fog minor design changes using additive manufacturing were made within one month. The GE9X conducted icing tests in Winter 2017. This engine completed 375 cycles in 335 hours run-time, which validated the engine design in terms of aerodynamic performance, mechanical system behaviour and secondary air system heat management. The first engine to test (FETT) completed its first run in April 2016. Because of the delays, the first flight test occurred in March 2018, with certification expected in late 2019. The first engine was expected to be ground-tested in 2016, with flight testing to begin in 2017 and certification happening in 2018. The engine for the 777-8X was to be derated to 88,000 lbf (390 kN). It was to feature the same 128 in (325 cm) fan diameter as the GE90-115B with thrust decreased by 15,800 lbf (70 kN) to a new rating of 99,500 lbf (443 kN) per engine. In February 2012, GE announced studies on a more efficient derivative of the GE90, calling it the GE9X, to power both the -8/9 variants of the new Boeing 777X. It is rated at 110,000 lbf (490 kN) of thrust, which is 5,000 lbf (20 kN) less than the GE90 highest thrust variant, the GE90-115, rated at 115,000 lbf (510 kN).

Derived from the General Electric GE90 with a larger fan, advanced materials like ceramic matrix composites (CMCs), and higher bypass and compression ratios, it was designed to improve fuel efficiency by 10% compared to the GE90. It received its Federal Aviation Administration (FAA) type certificate on September 25, 2020.

It first ran on the ground in April 2016 and first flew on Mait powered the 777-9's maiden flight in early 2020. The General Electric GE9X is a high-bypass turbofan developed by GE Aerospace exclusively for the Boeing 777X. General Electric GE90, General Electric GEnx GE9X installed on the 777X during roll-out in March 2019 For the similarly-named engine which powers the Boeing 787, see General Electric GEnx.
